In the realm of sports facility construction, the durability and longevity of surfaces are paramount considerations. Prefabricated rubber tracks have gained popularity not only for their comfort and safety benefits but also for their resilience against various environmental factors, including UV radiation. This article explores the UV resistance capabilities of prefabricated rubber tracks, highlighting their importance and the technology behind their design.
Understanding UV Radiation
Ultraviolet (UV) radiation from the sun poses a significant challenge to outdoor materials, including sports surfaces. UV rays can cause materials to degrade over time, leading to color fading, surface cracking, and reduced structural integrity. For sports facilities exposed to sunlight throughout the year, such as running tracks, playgrounds, and outdoor courts, UV resistance is crucial for maintaining performance and aesthetic appeal.
Engineering UV-Resistant Rubber Tracks
Prefabricated rubber tracks are engineered with specialized formulations and additives to enhance their UV resistance. Manufacturers incorporate UV stabilizers into the rubber compound during production. These stabilizers act as shields, absorbing and dissipating UV radiation before it can penetrate and degrade the rubber material. By mitigating UV-induced degradation, these tracks maintain their color vibrancy and structural integrity over prolonged exposure periods.
Benefits of UV Resistance
The UV resistance of prefabricated rubber tracks extends their lifespan and reduces maintenance requirements. Tracks that retain their color and elasticity are more aesthetically pleasing and safer for athletes. The consistent performance of UV-resistant tracks ensures reliable traction and shock absorption, contributing to optimal athletic experiences and reducing the risk of injuries.
Testing and Standards
To assess and verify UV resistance, prefabricated rubber tracks undergo rigorous testing according to international standards. These tests simulate long-term exposure to UV radiation under controlled conditions, evaluating factors such as color retention, surface integrity, and material strength. Compliance with these standards ensures that tracks meet performance expectations and remain durable in outdoor environments.
Prefabricated Rubber Running Track Application
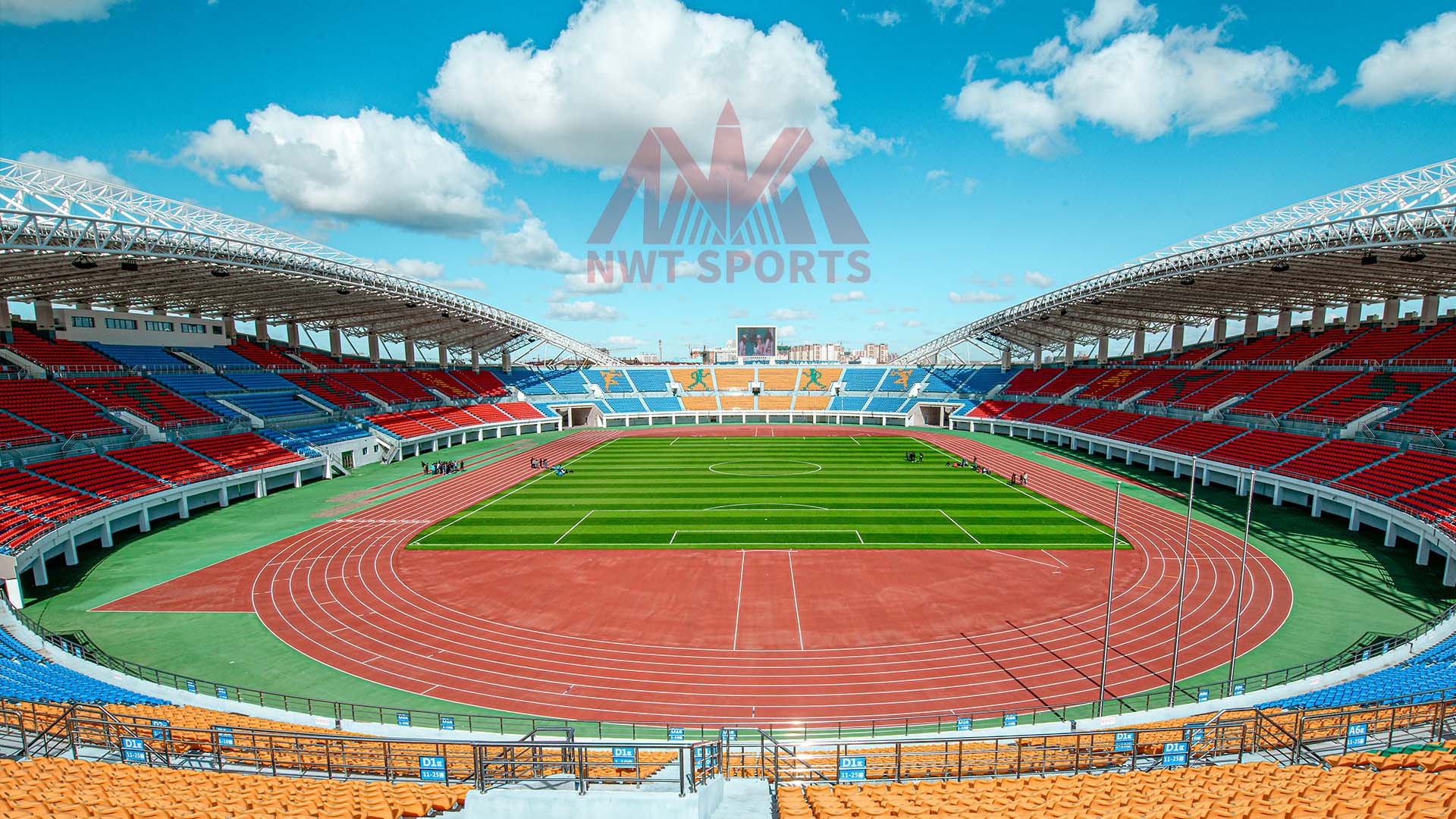
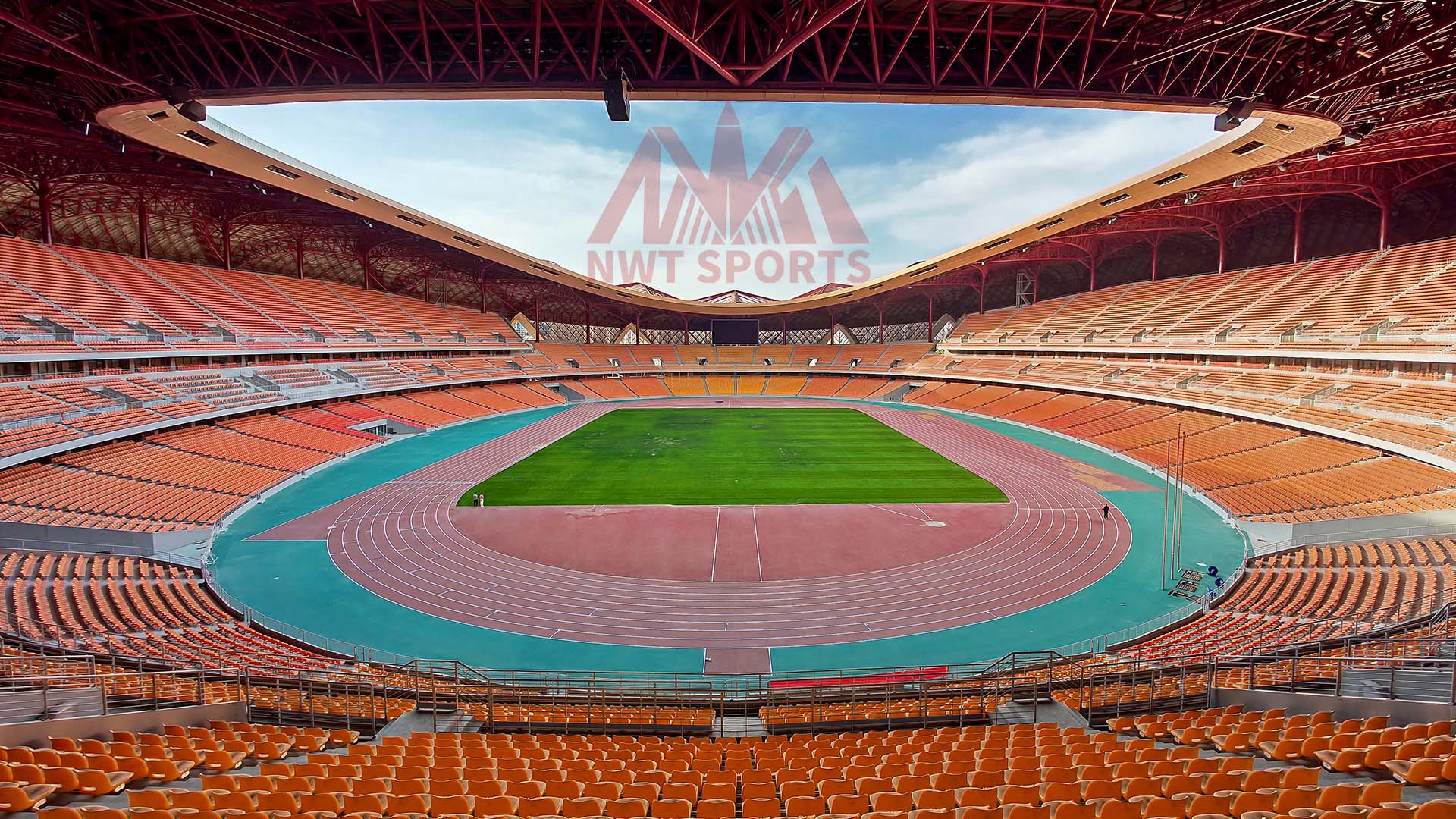
Environmental Considerations
Beyond performance, UV-resistant rubber tracks contribute to environmental sustainability. By maintaining their structural integrity and aesthetics over extended periods, these tracks reduce the frequency of replacements and minimize waste. The use of recycled rubber materials in track construction further enhances their eco-friendly profile, aligning with sustainable development goals.
Conclusion
In conclusion, the UV resistance of prefabricated rubber tracks plays a crucial role in their suitability for outdoor sports facilities. By integrating advanced UV stabilizers and adhering to stringent testing standards, manufacturers ensure that these tracks withstand the challenges posed by UV radiation. This resilience not only extends the lifespan of sports surfaces but also enhances safety, performance, and environmental sustainability. Prefabricated rubber tracks continue to evolve as a preferred choice for schools, communities, and professional sports venues seeking durable, high-performance surfaces capable of withstanding the elements while supporting athletic excellence.
This focus on UV resistance underscores the commitment of manufacturers to innovation and sustainability in sports facility design and construction.
Prefabricated Rubber Running Track Color Card

Prefabricated Rubber Running Track Structures
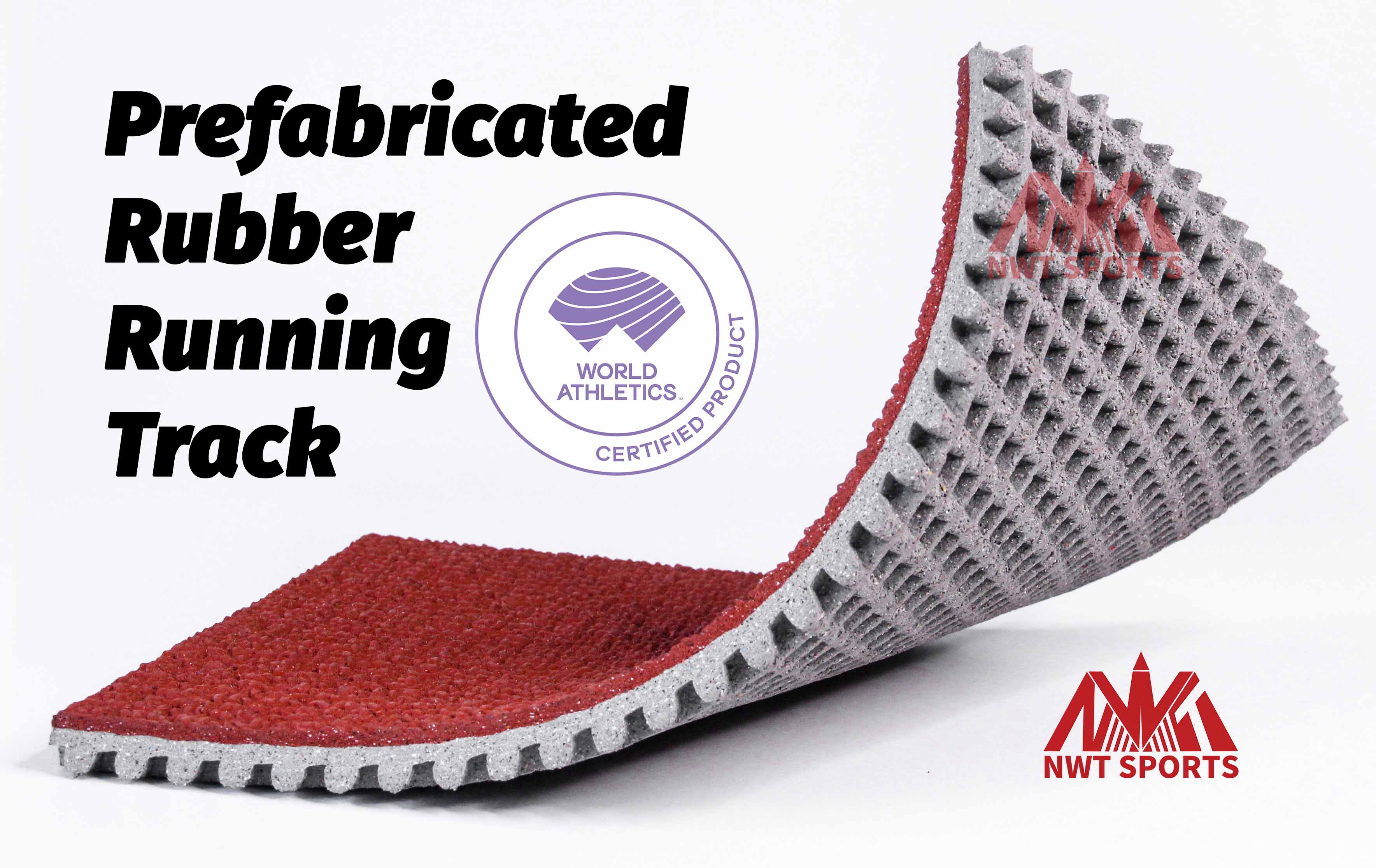
Our product is suitable for higher education institutions, sports training centers, and similar venues. The key differentiator from 'Training Series' lies in its lower layer design, which features a grid structure, offering a balanced degree of softness and firmness. The lower layer is designed as a honeycomb structure, which maximizes the degree of anchoring and compaction between the track material and the base surface while transmitting the rebound force generated at the moment of impact to the athletes, thereby effectively reducing the impact received during exercise, and This is transformed into forwarding kinetic energy, which improves the athlete's experience and performance.This design maximizes the compactness between the track material and the base, efficiently transmitting the rebound force generated during impacts to athletes, converting it into forward kinetic energy. This effectively reduces the impact on joints during exercise, minimizes athlete injuries, and enhances both training experiences and competitive performance.
Prefabricated Rubber Running Track Details
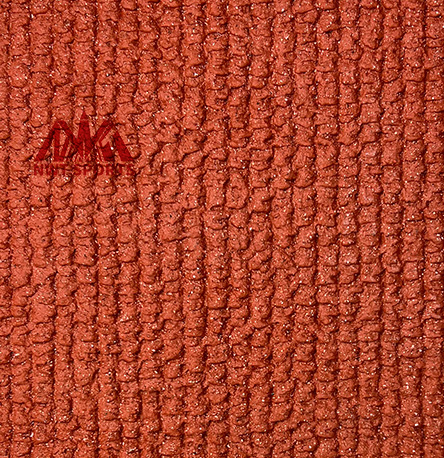
Wear-resistant layer
Thickness: 4mm ±1mm
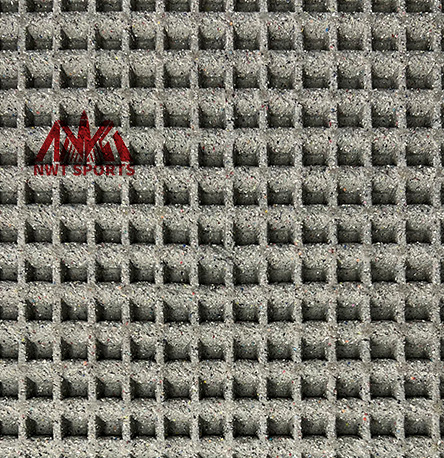
Honeycomb airbag structure
Approximately 8400 perforations per square meter

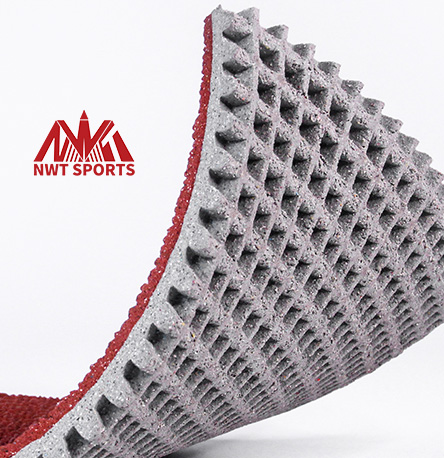
Elastic base layer
Thickness: 9mm ±1mm
Prefabricated Rubber Running Track Installation
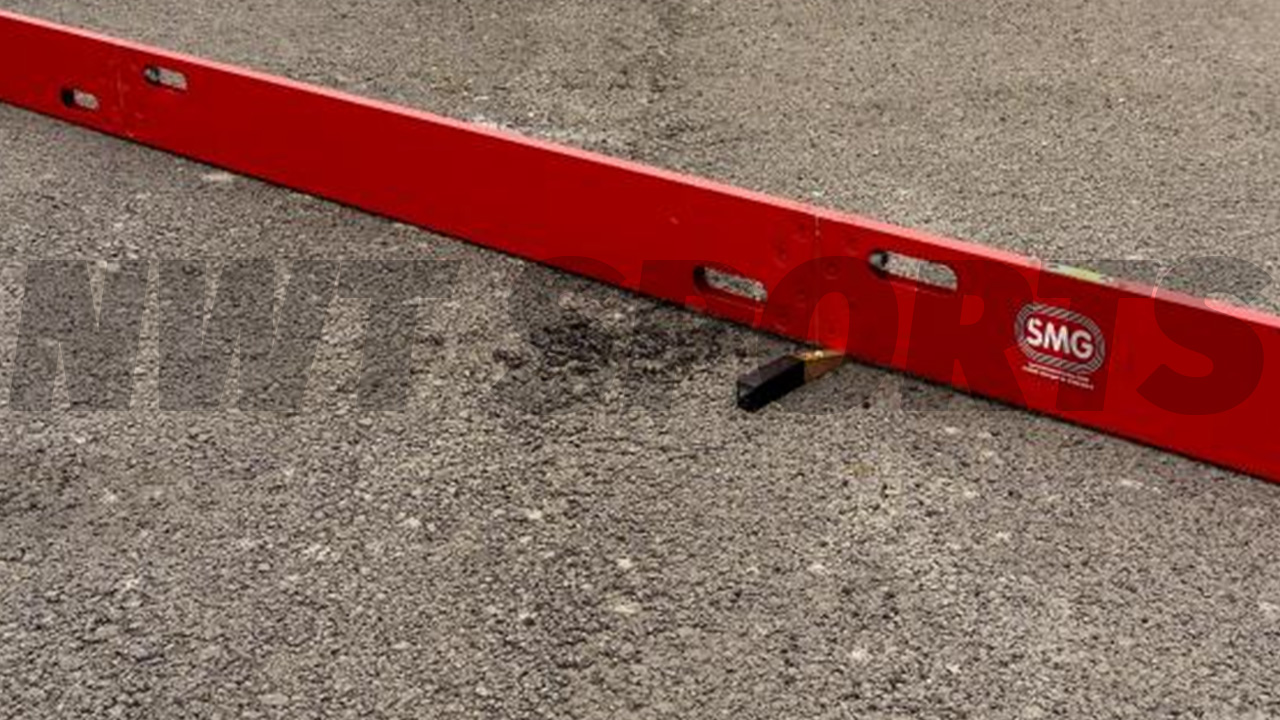
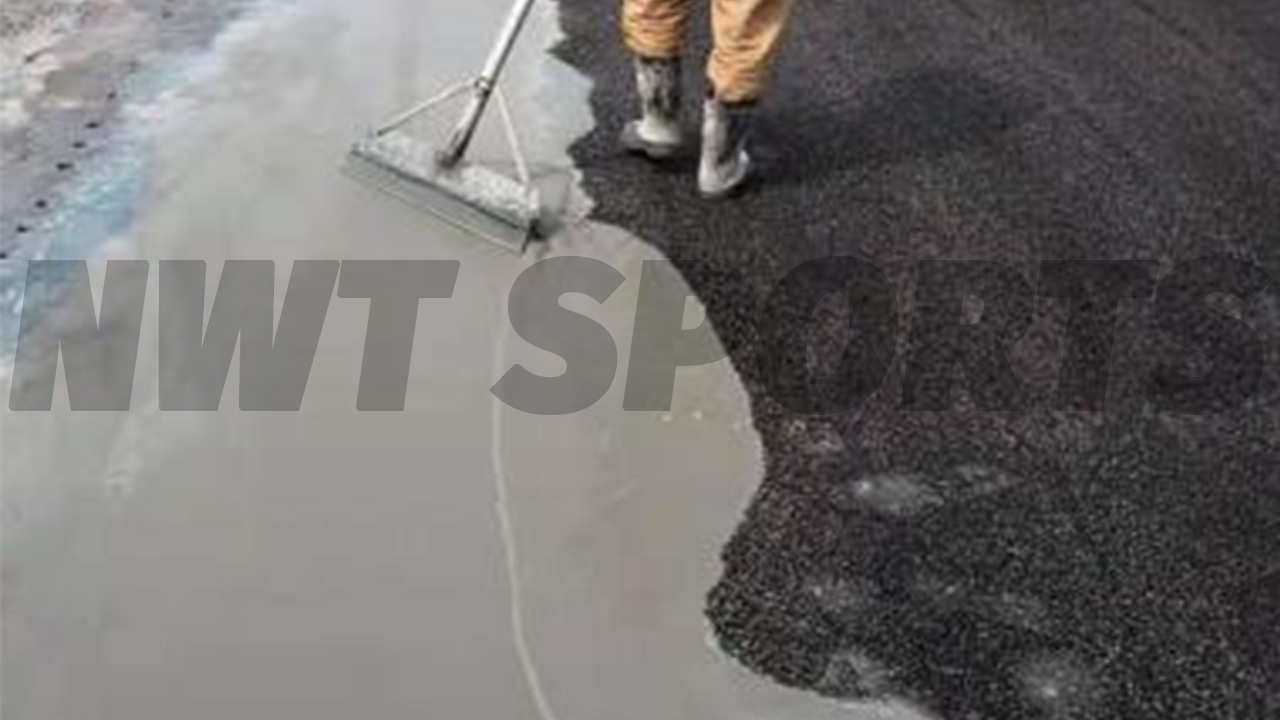
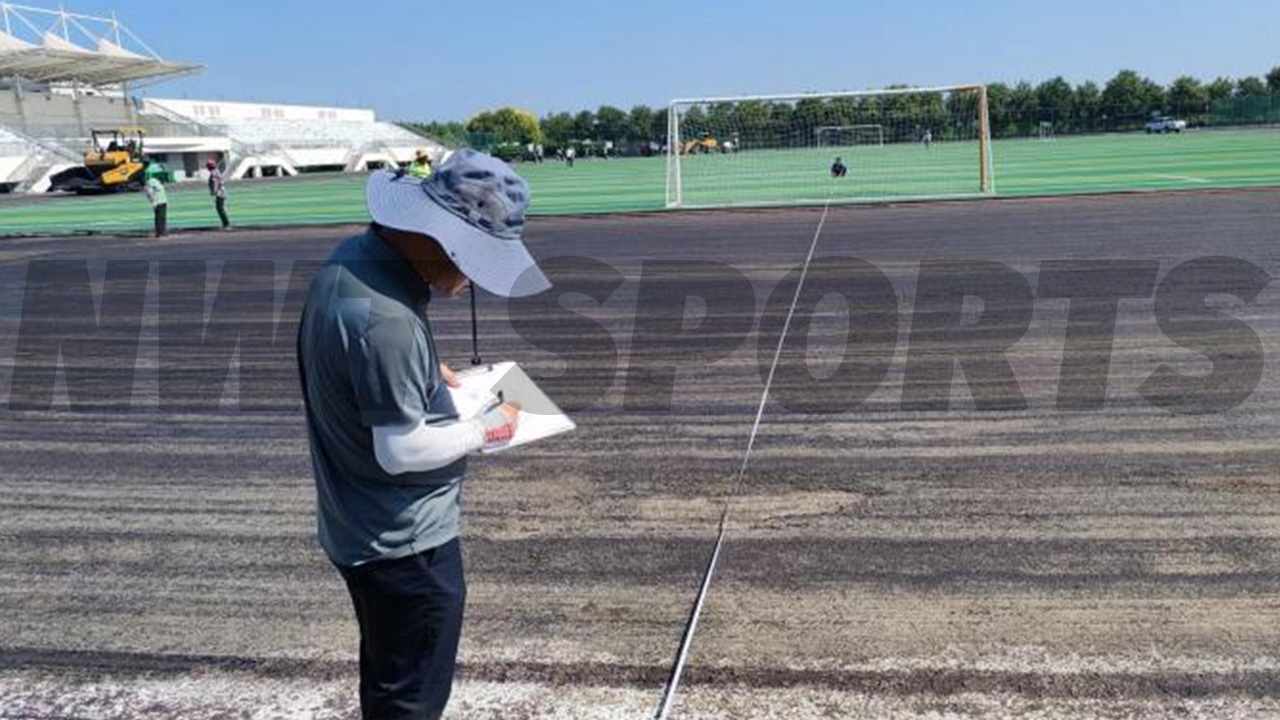
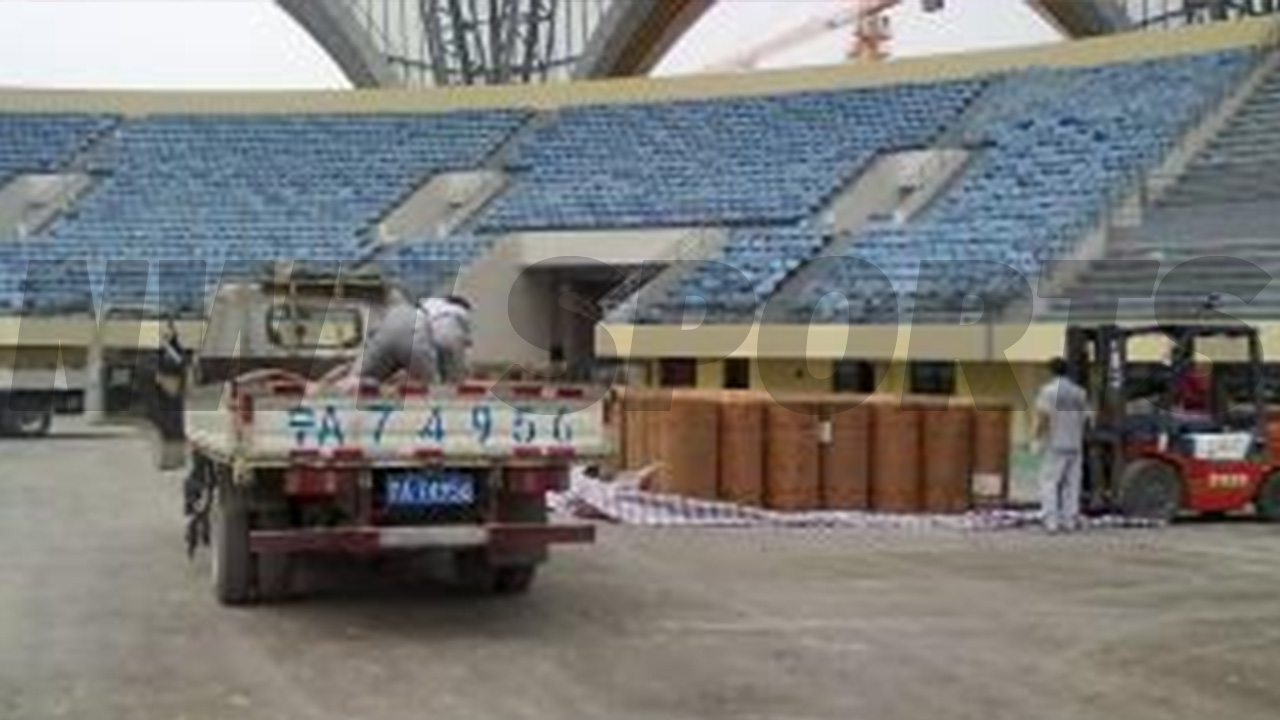
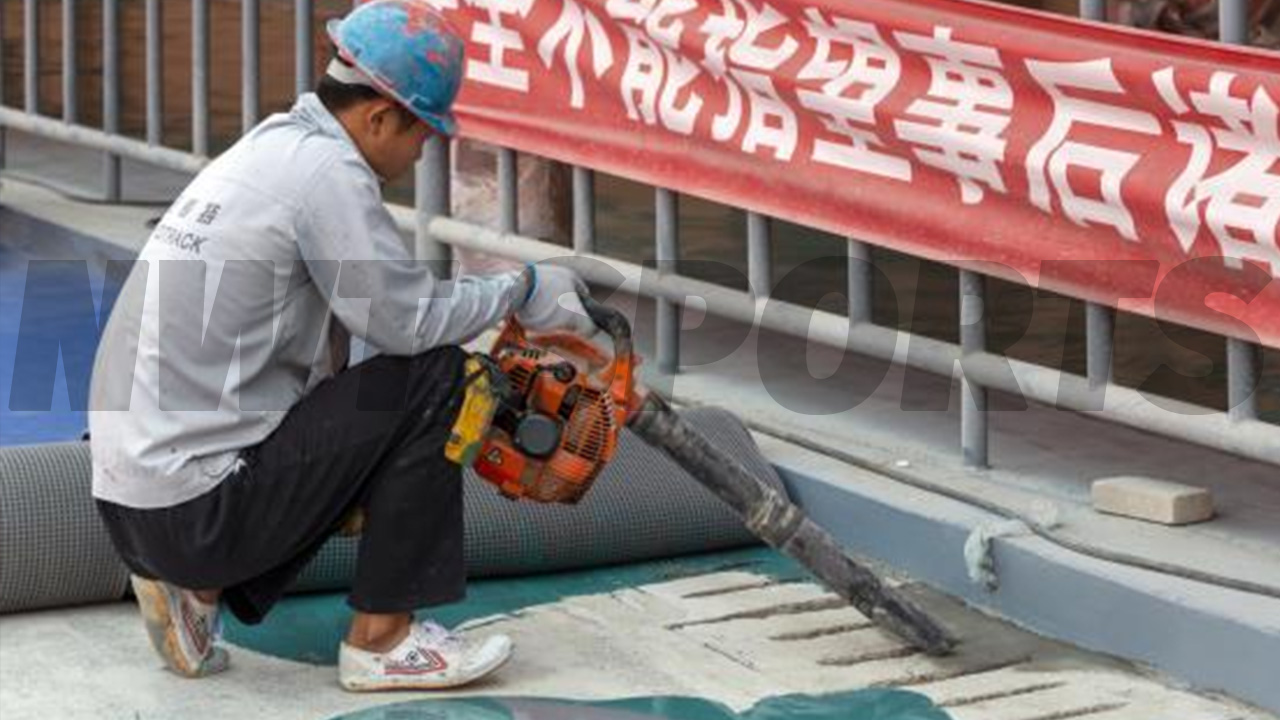
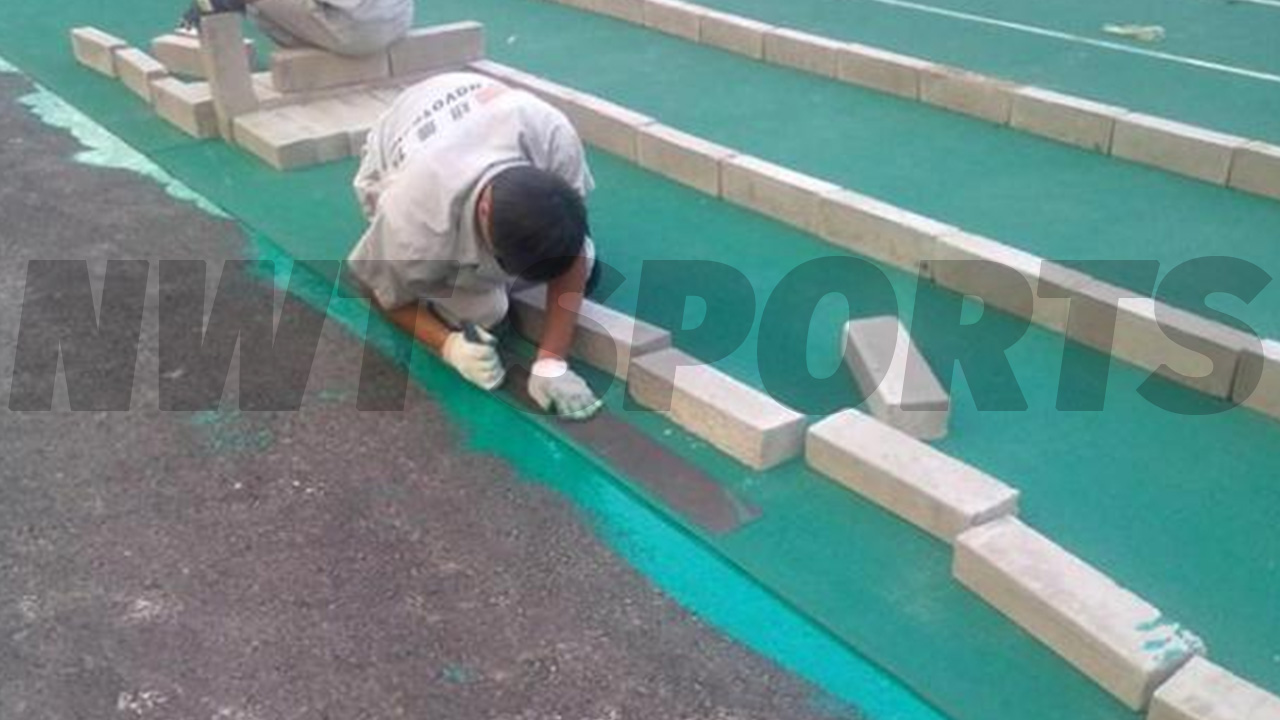
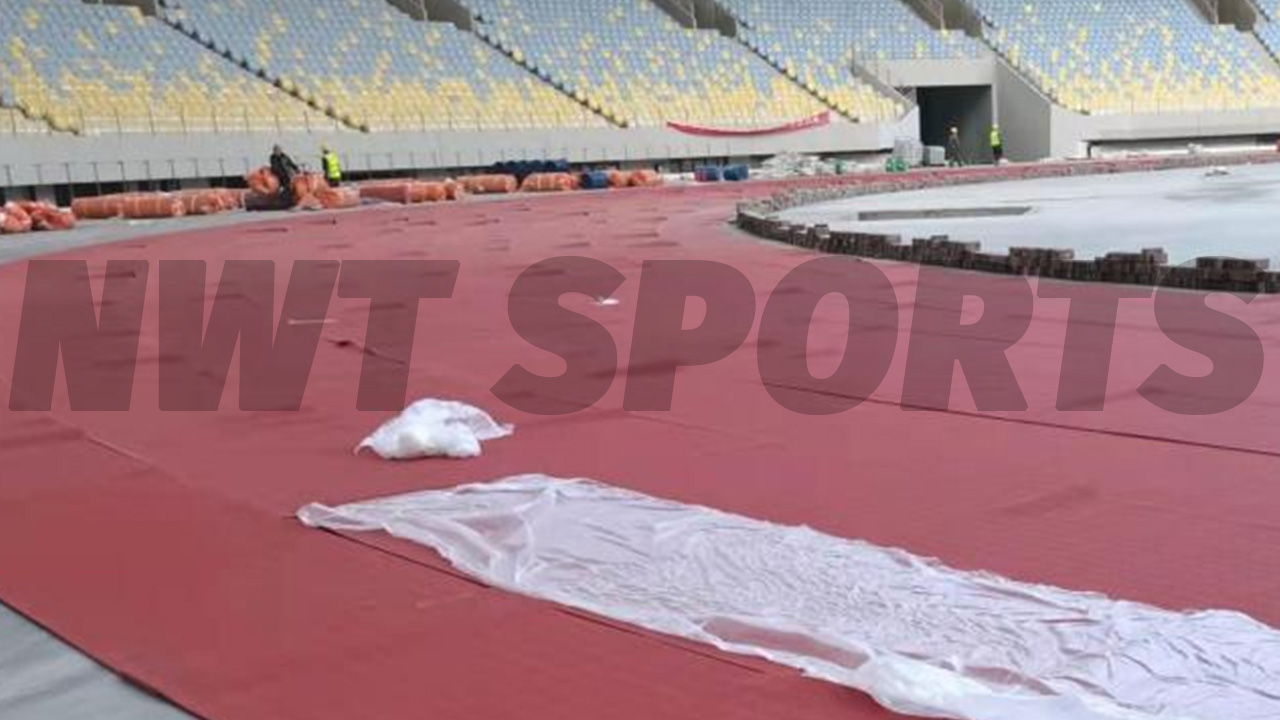

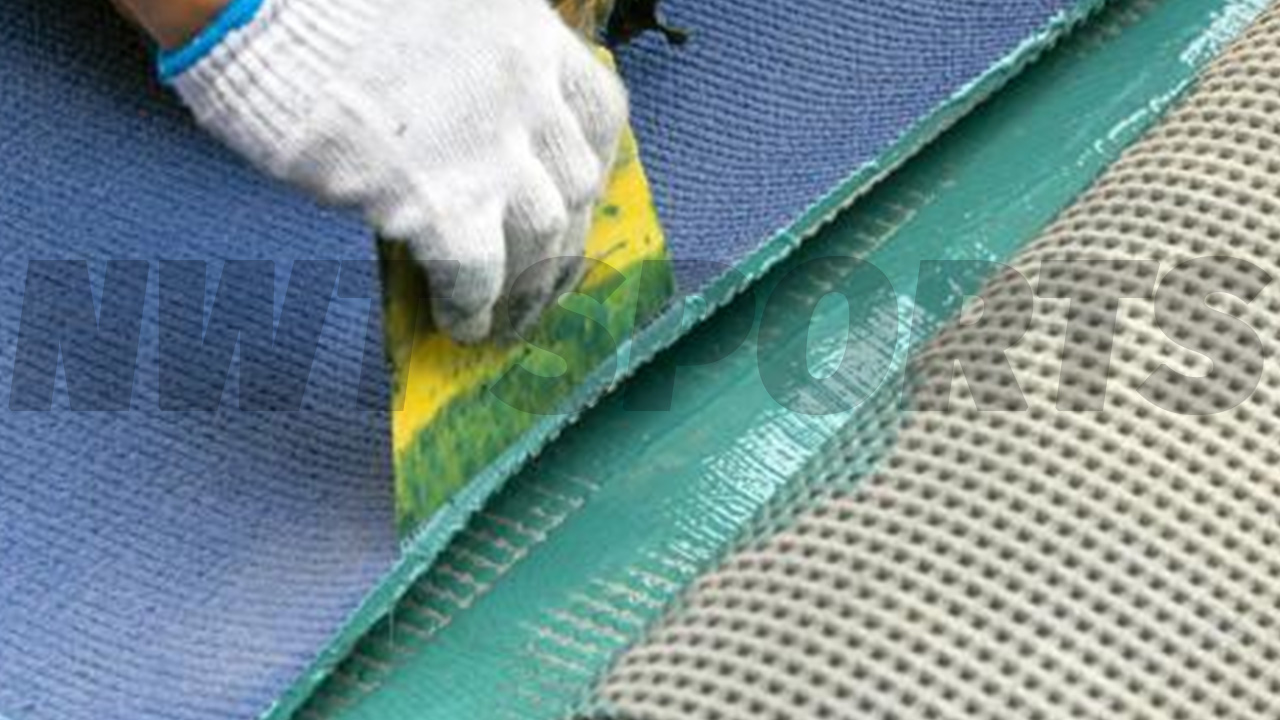
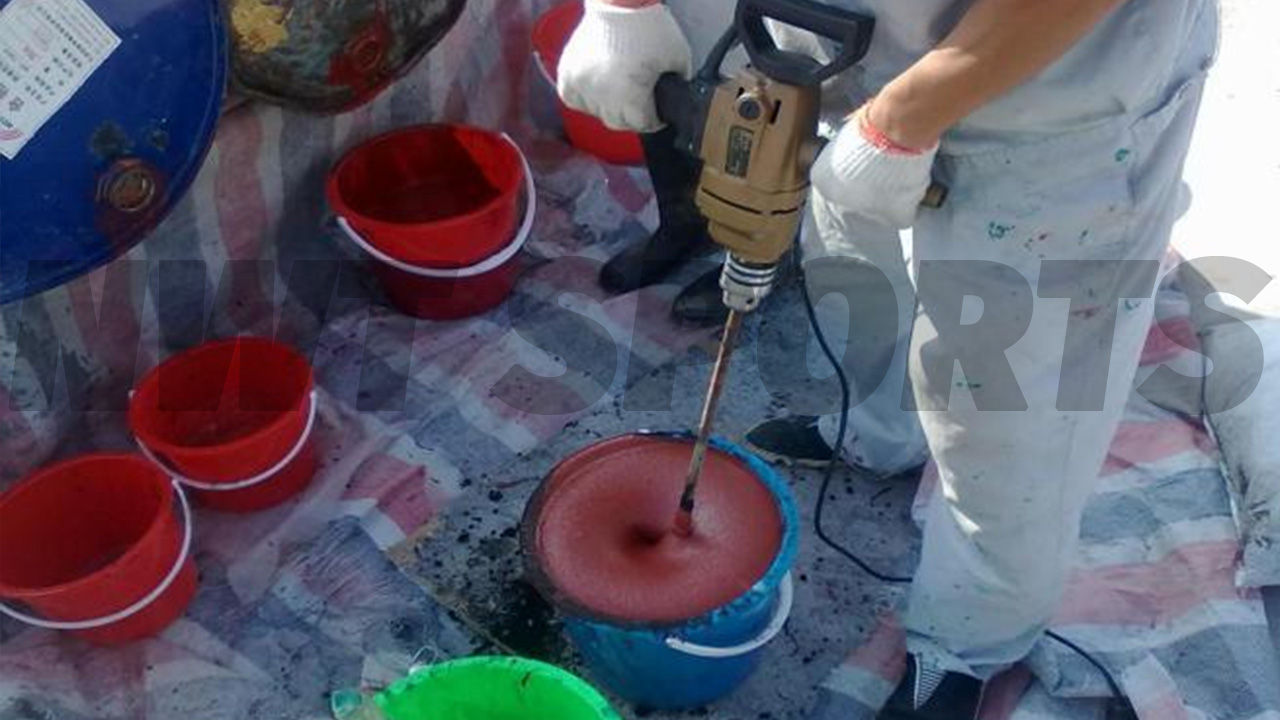
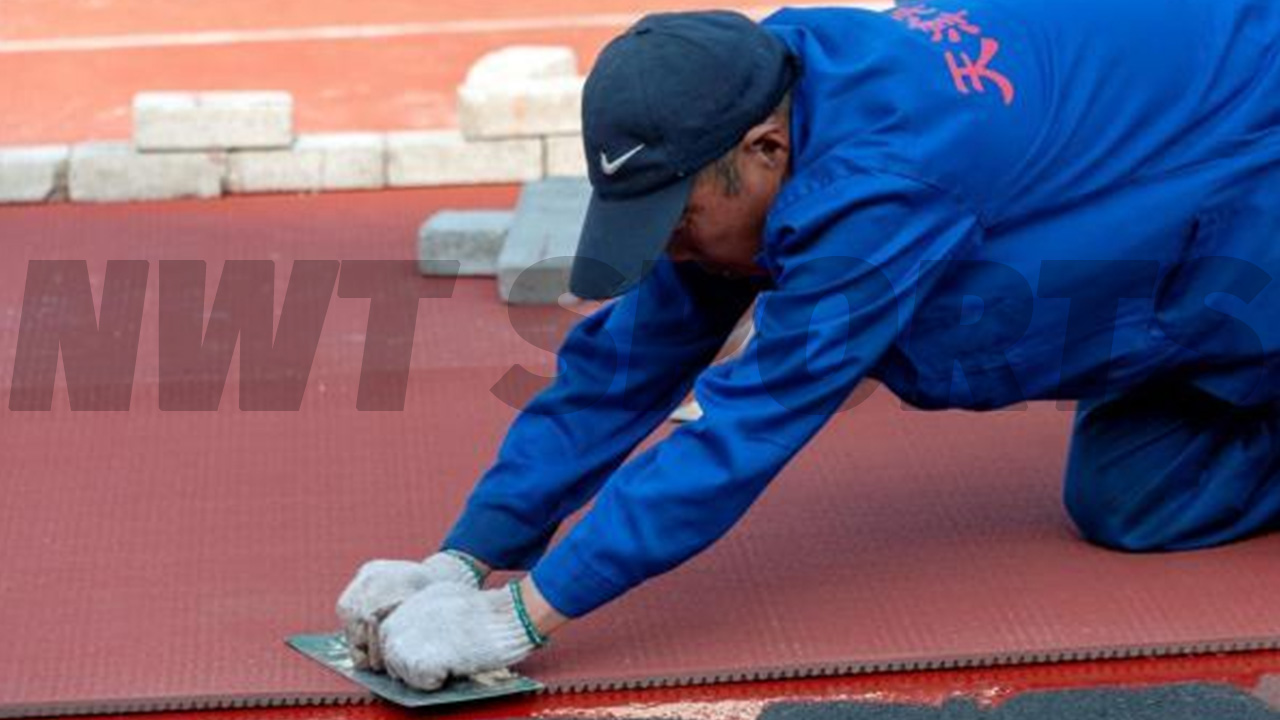
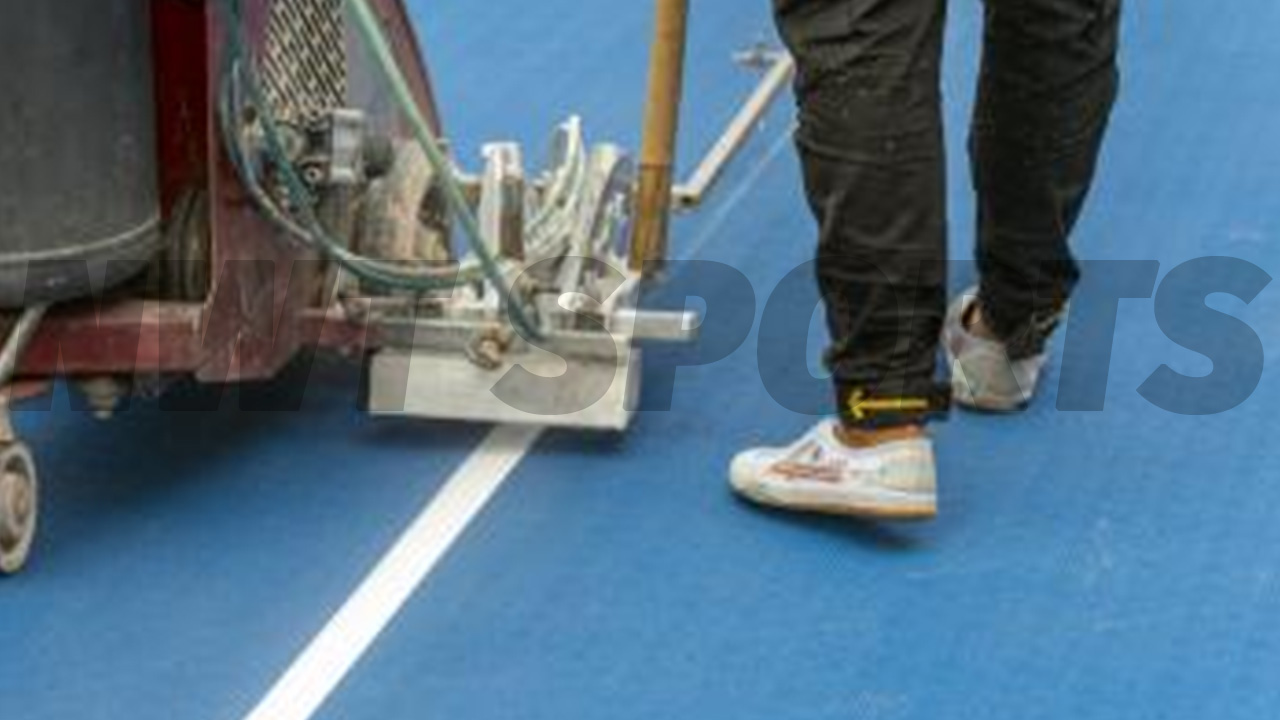
Post time: Jul-05-2024