NWT Sports, a leading name in running track installation companies, specializes in creating high-quality, durable tracks for various venues. Whether you need a synthetic track for a school, a professional 400m running track, or an indoor 200m track, we provide expert services tailored to your needs.
Step 1: Planning & Design
The first step in any running track installation is meticulous planning and design. At NWT Sports, we begin with a comprehensive site evaluation, analyzing factors such as terrain, drainage, and accessibility. This allows us to create a customized design that meets the specific needs of your venue. Whether it's a standard 400m running track or a custom layout for a smaller space, our designs prioritize both functionality and longevity.
Step 2: Site Preparation
Proper site preparation is crucial for the success of any running track. This stage involves clearing the site of debris and vegetation, followed by the installation or enhancement of drainage systems to prevent waterlogging. A well-prepared site ensures the durability and performance of the track, making it essential for long-term use.
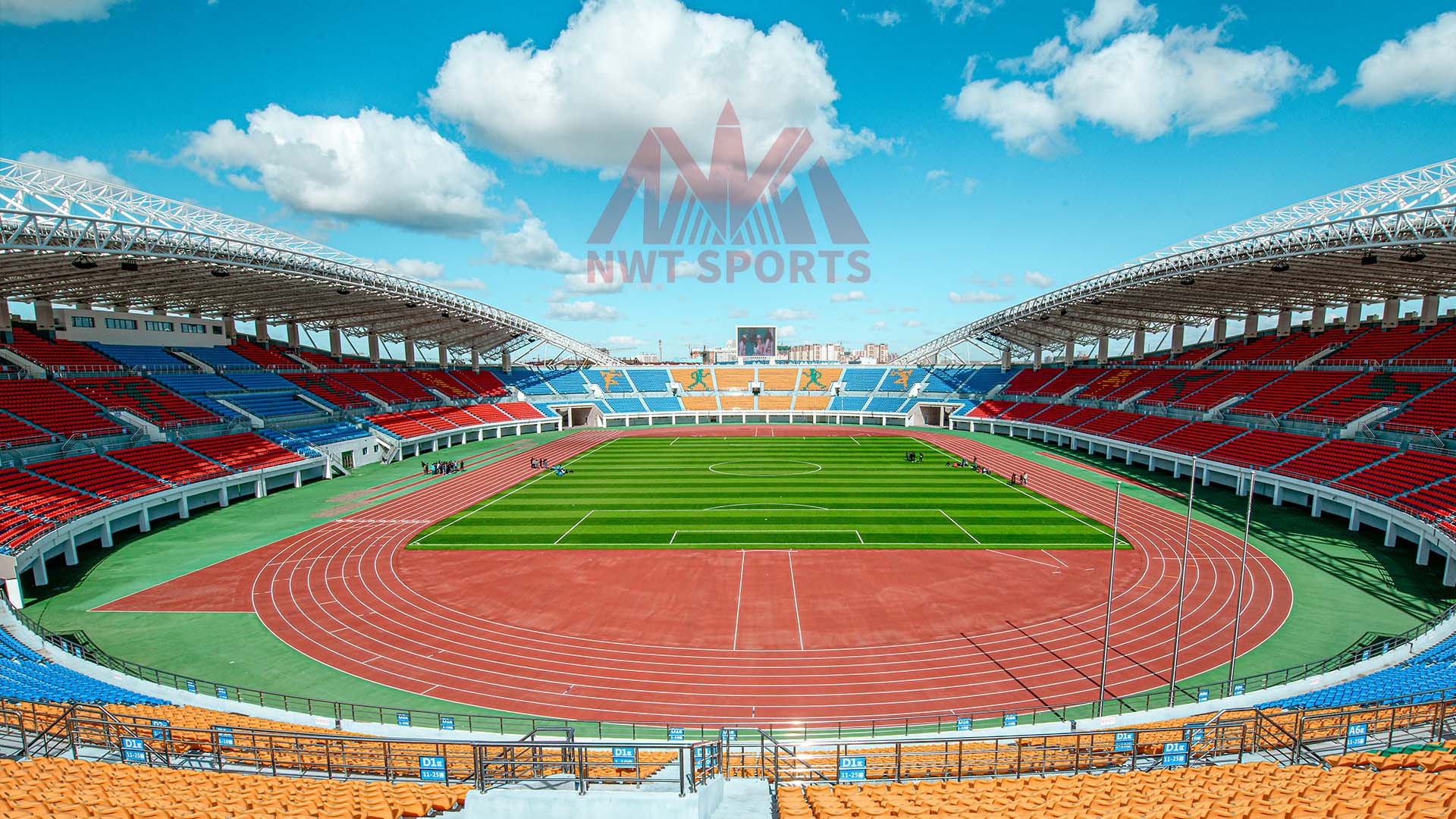
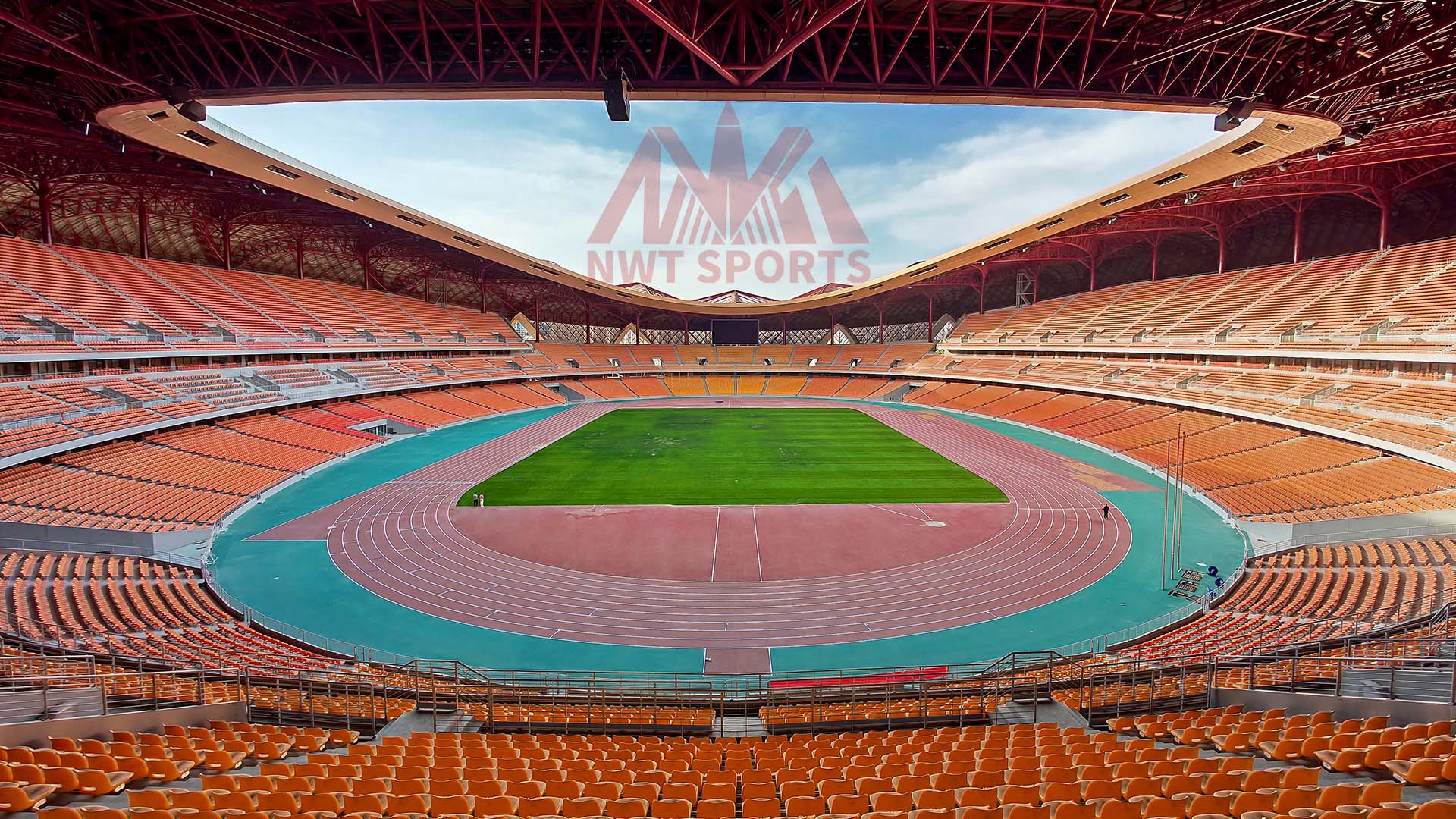
Step 3: Base Construction
The foundation of a running track is as important as the surface itself. NWT Sports uses high-quality materials like crushed stone or aggregate to create a stable base. This base is carefully graded and compacted to provide the necessary support for the synthetic track surface. A well-constructed base is key to preventing future issues such as cracks or uneven surfaces.
Prefabricated Rubber Running Track Color Card

Step 4: Synthetic Track Surface Installation
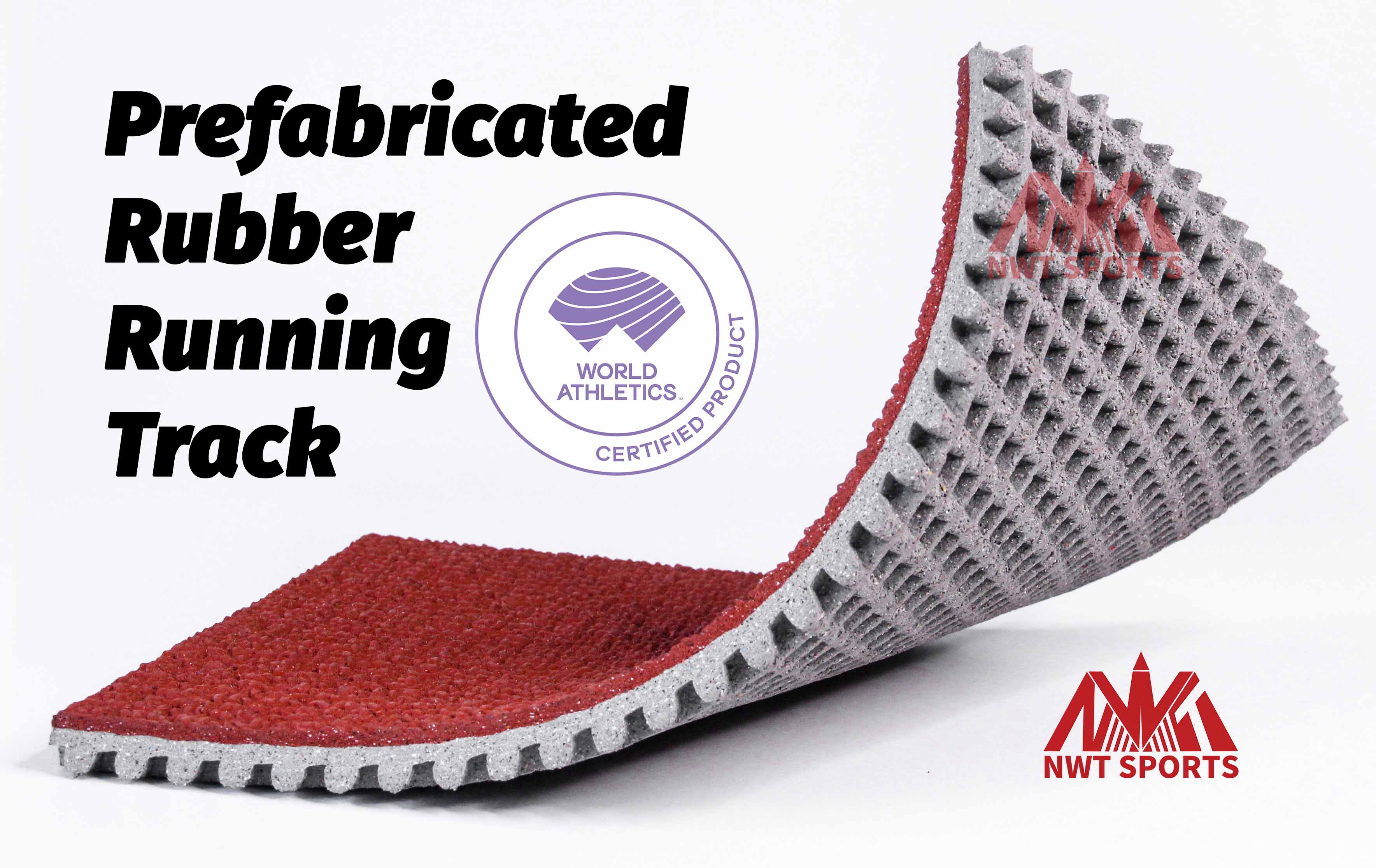
Once the base is ready, we proceed with the installation of the synthetic track surface. This involves applying multiple layers of polyurethane or rubber, each layer meticulously spread and compacted to create a resilient and durable surface. The synthetic track surface is designed to provide athletes with optimal traction, cushioning, and speed, making it ideal for both training and competitive events.
Step 5: Marking & Finishing
After the synthetic track surface is in place, the final steps involve marking the lanes and applying a finishing treatment. The lane markings are applied according to international or national standards, ensuring the track is ready for competitive use. The finishing treatment enhances the track's slip resistance and overall durability, ensuring it can withstand the rigors of daily use.
Conclusion
Running track installation is a complex process that requires expertise, precision, and attention to detail. NWT Sports is committed to delivering turnkey solutions that meet the specific needs of any venue, ensuring top performance and long-lasting quality. From planning and design to installation and finishing, we handle every aspect of the process, making us one of the top running track installation companies in the industry.
Prefabricated Rubber Running Track Details
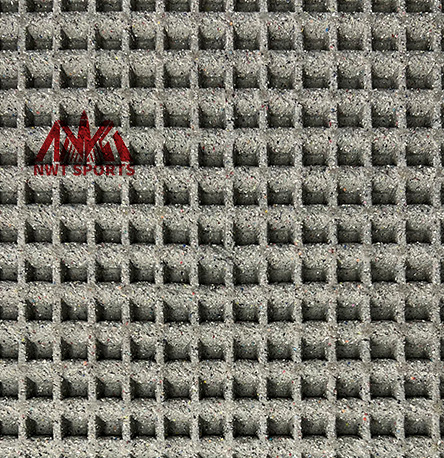
Honeycomb airbag structure
Approximately 8400 perforations per square meter

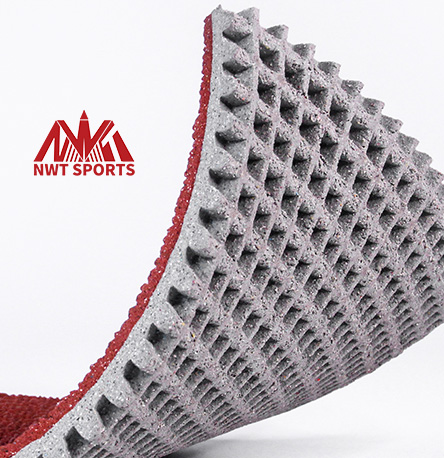
Elastic base layer
Thickness: 9mm ±1mm
Prefabricated Rubber Running Track Installation
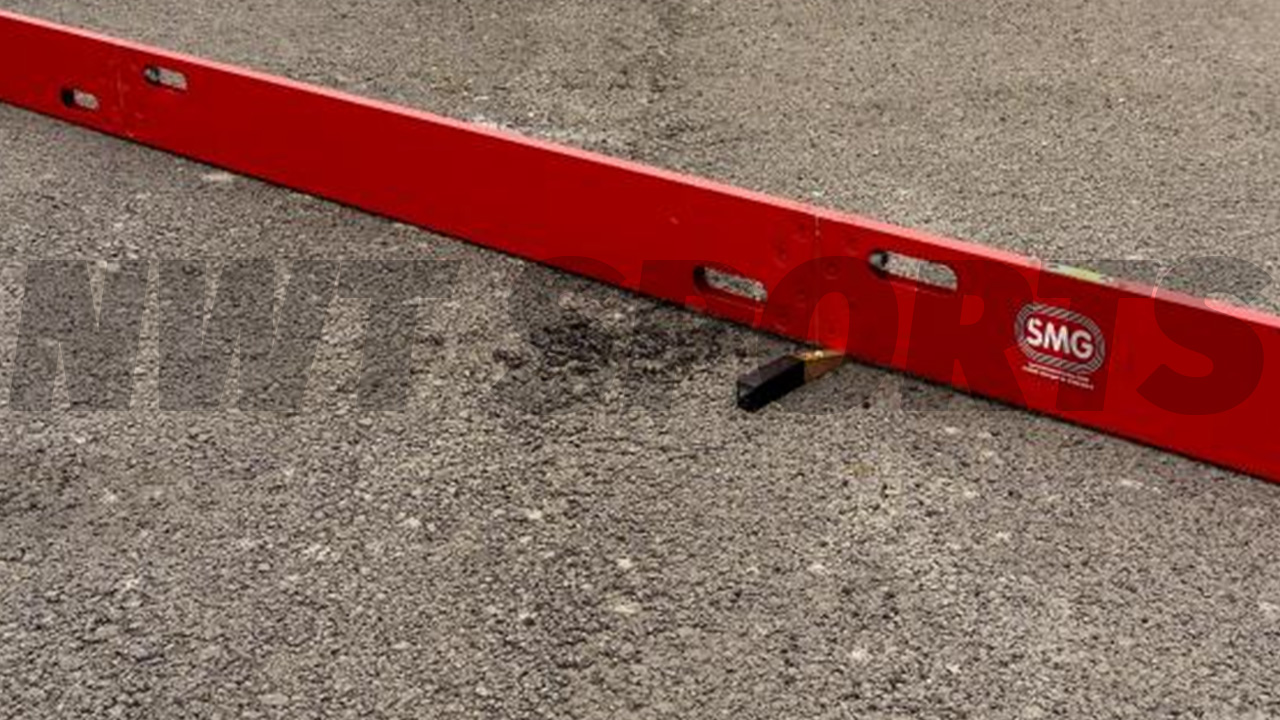
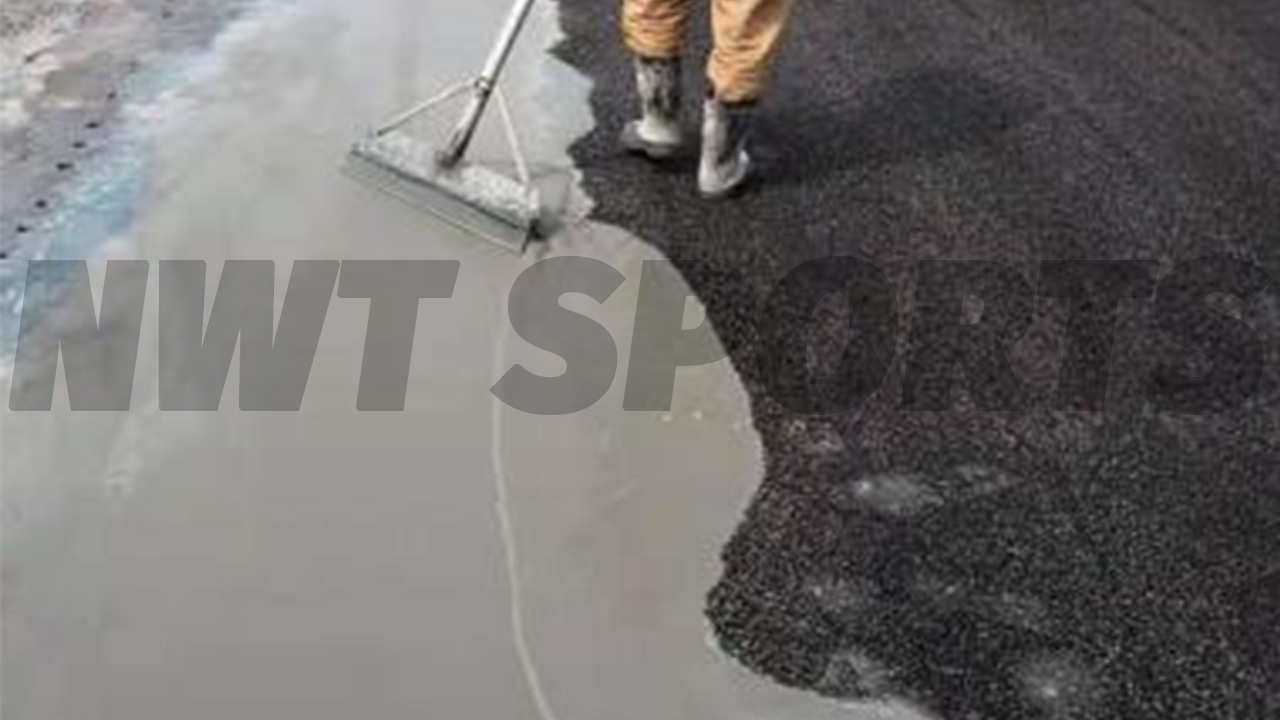
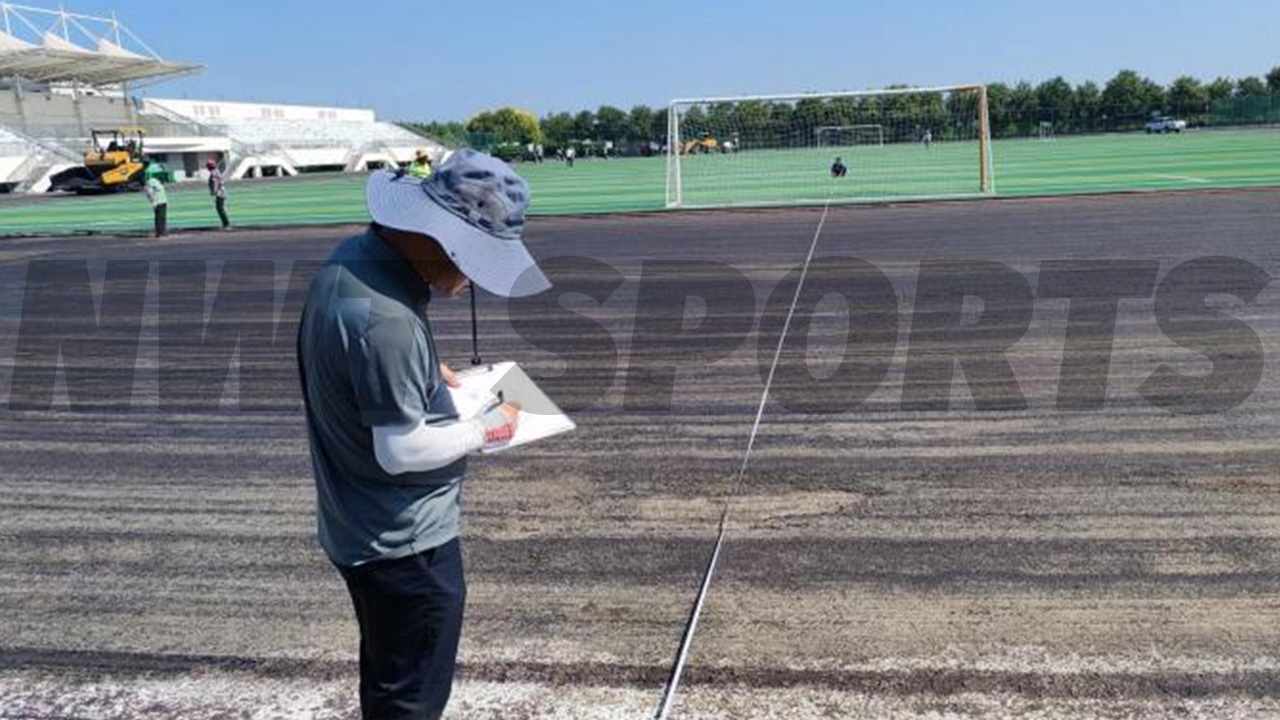
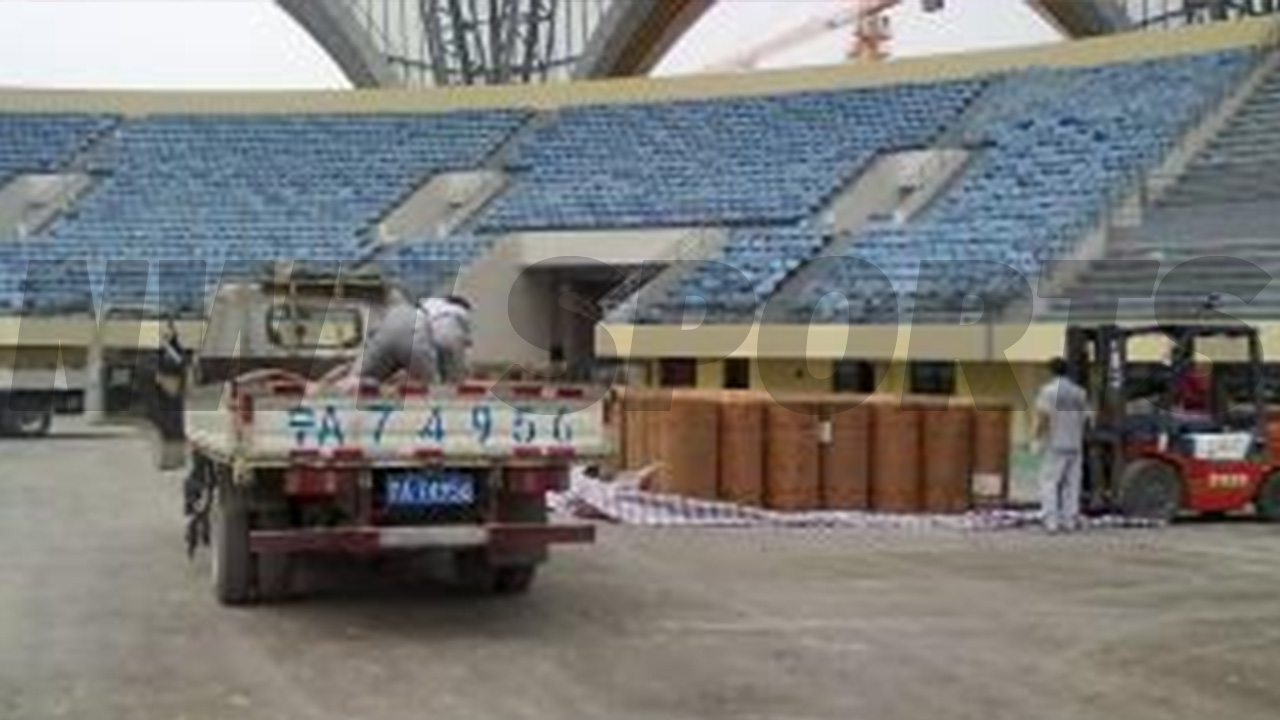
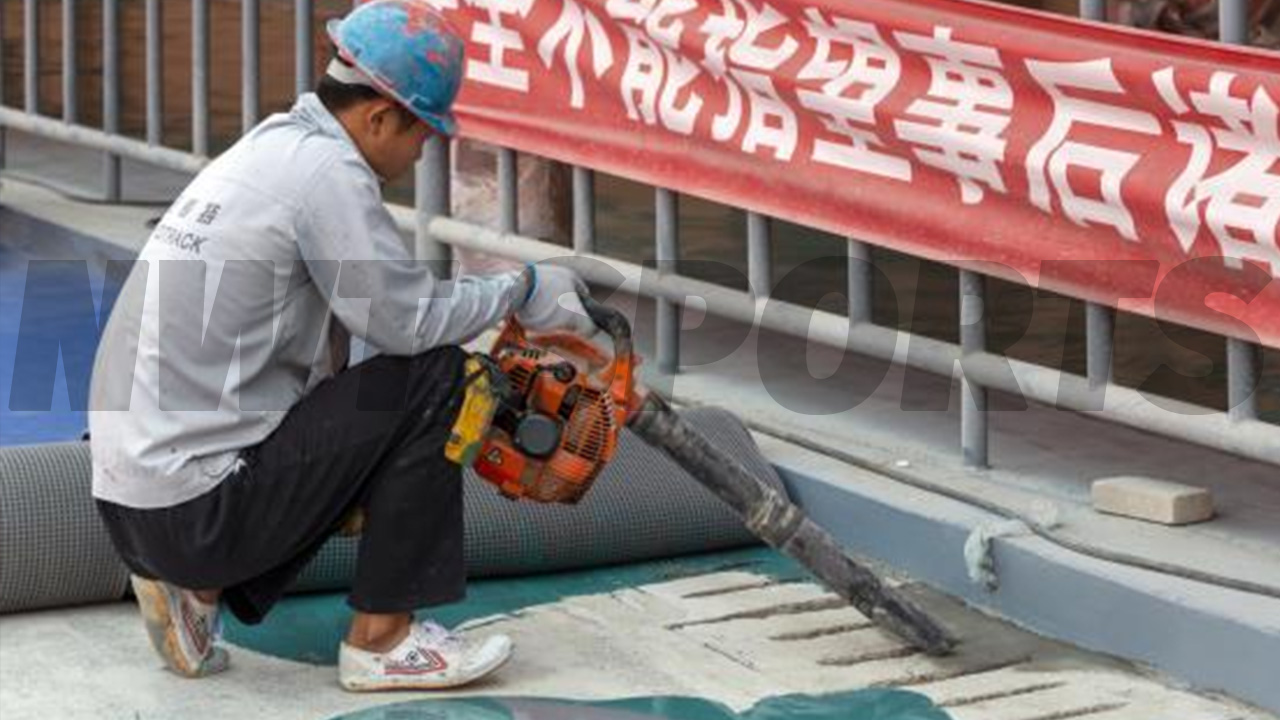
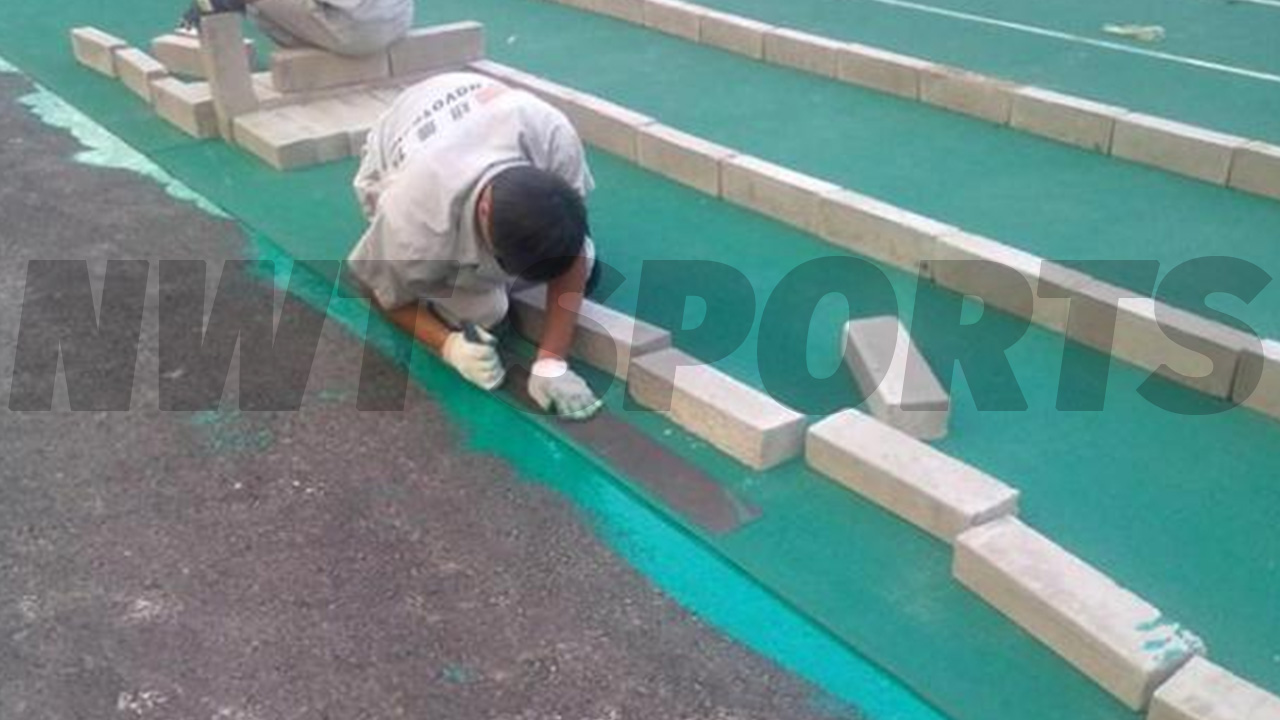
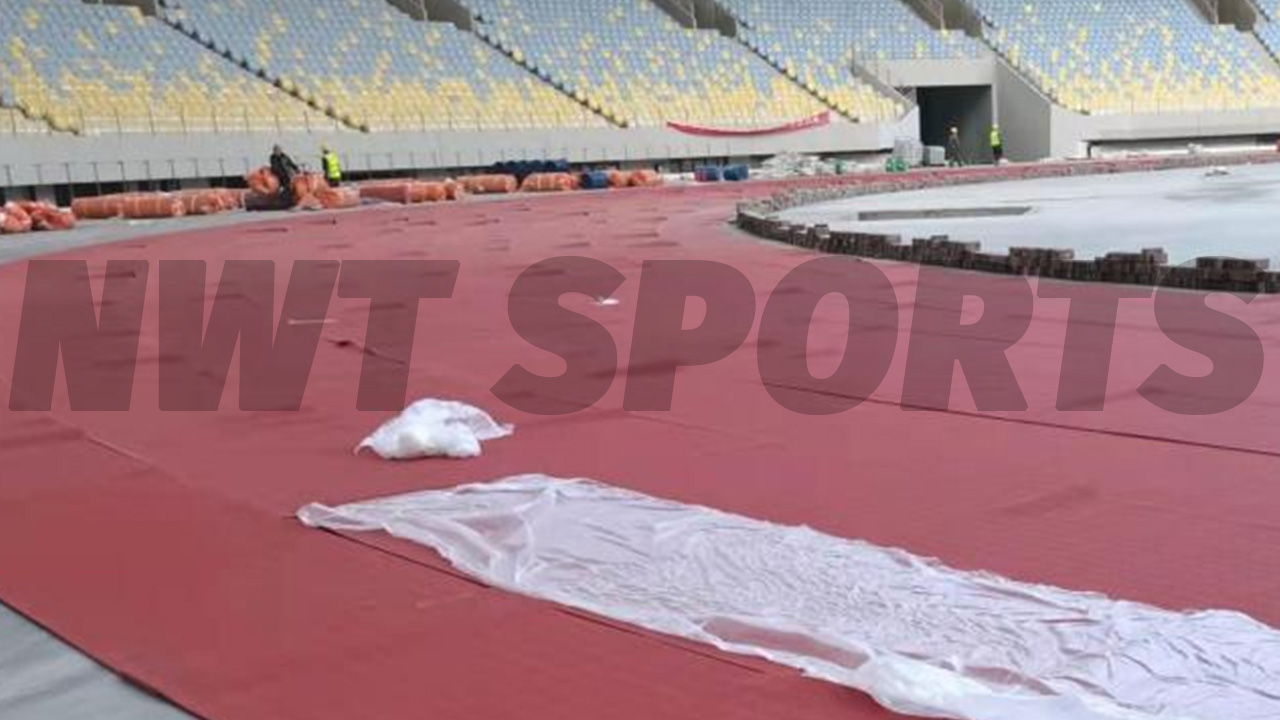

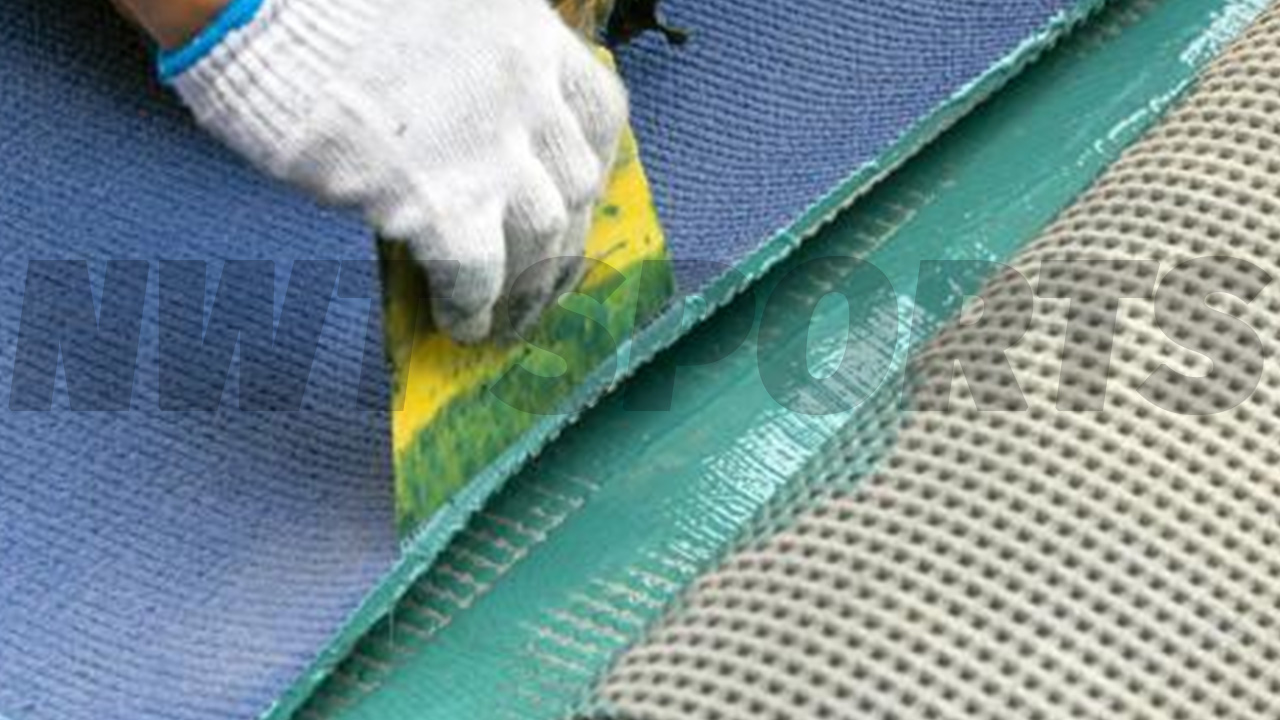
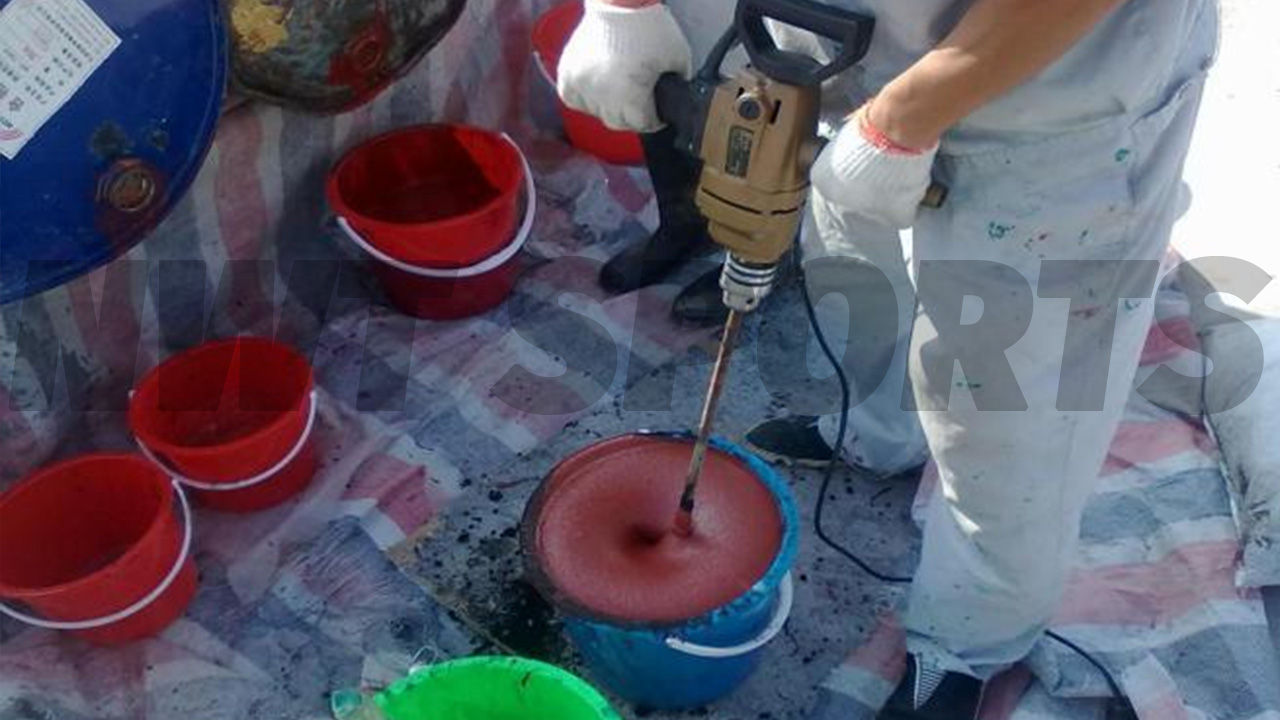
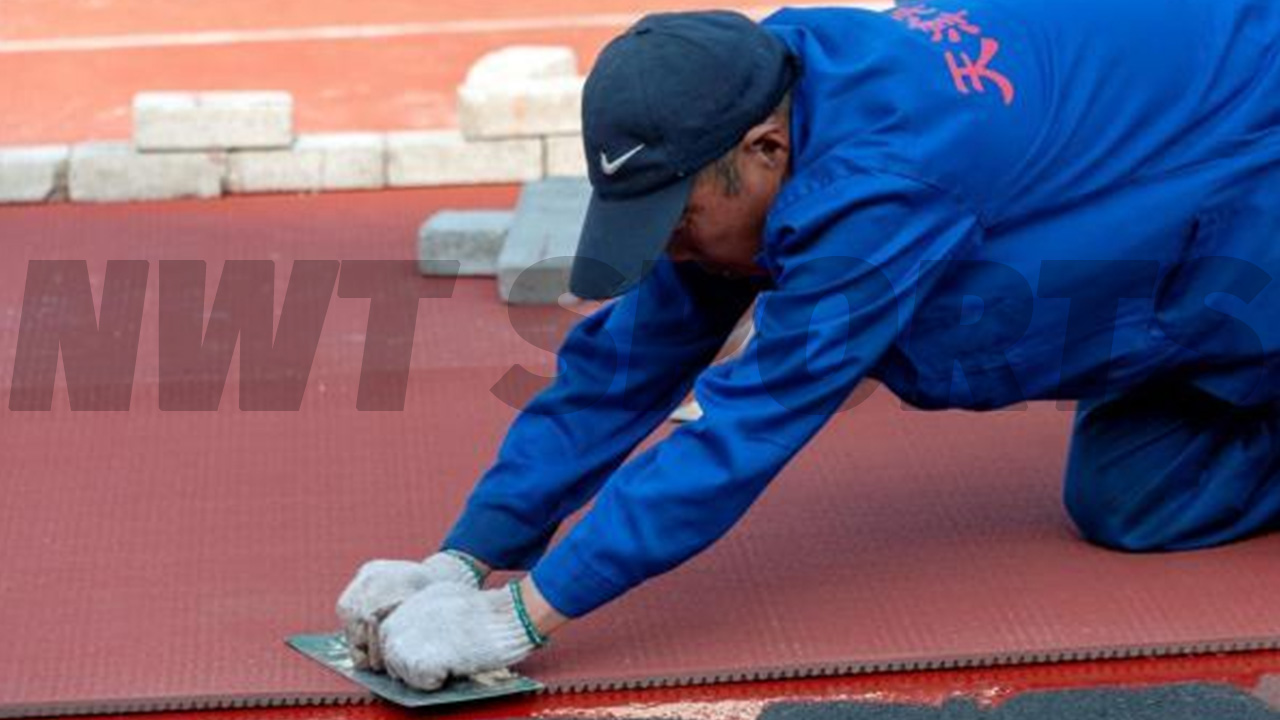
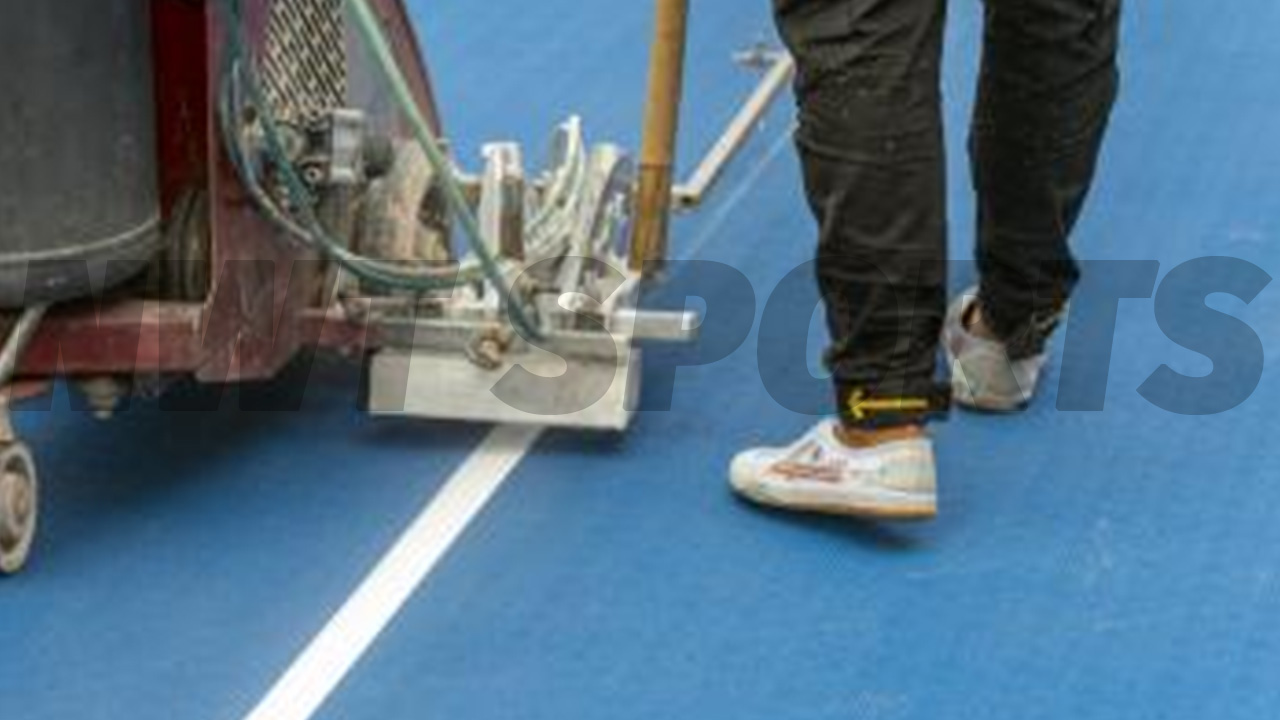
Post time: Aug-30-2024